HydroGenesys
HydroGenesys
Hydrogenesys project
Waste Processing Technologies
from anything to H2… and more!
Current disposal methods
Landfills
Incinerators
Composting
Hydrogen: the current scenario
H2 Production
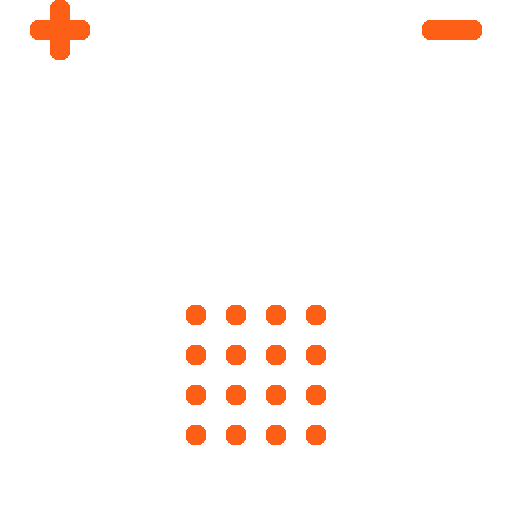
Electrolysis of water
- Highly energy-intensive process (high consumption of electricity to ensure the reaction)
- Use of large quantities of water (a resource that is becoming increasingly important)
- High cost of production (about 2,37 $ / Kg)
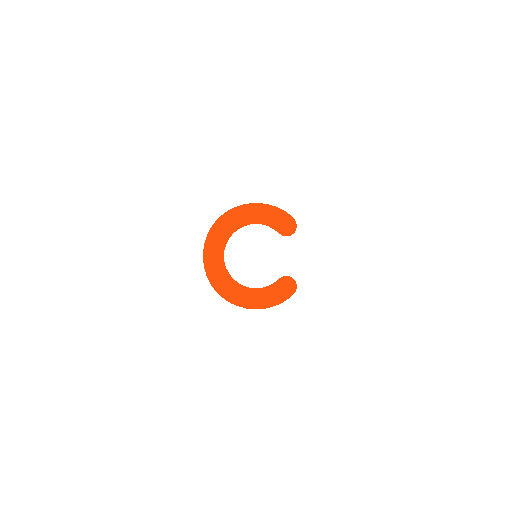
Methane steam reforming
- Process that involves the use of non-renewable fossil resources in high quantities (about 2Kg of CH4 for each Kg of H2)
- Reduced production cost (about $ 0.40 / Kg)
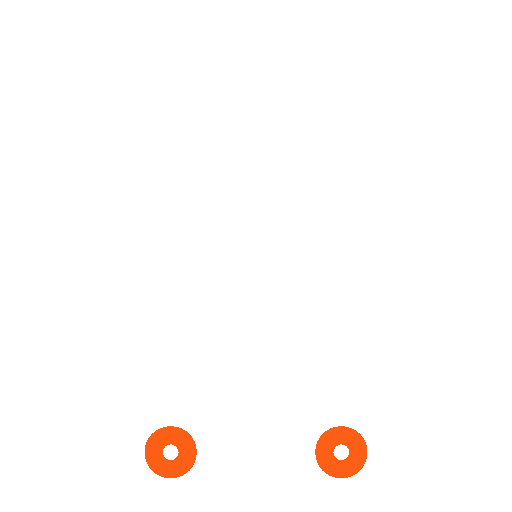
Coal gasification
- Process that involves the use of non-renewable fossil resources
- Low production cost (about 0,54 $ / Kg)
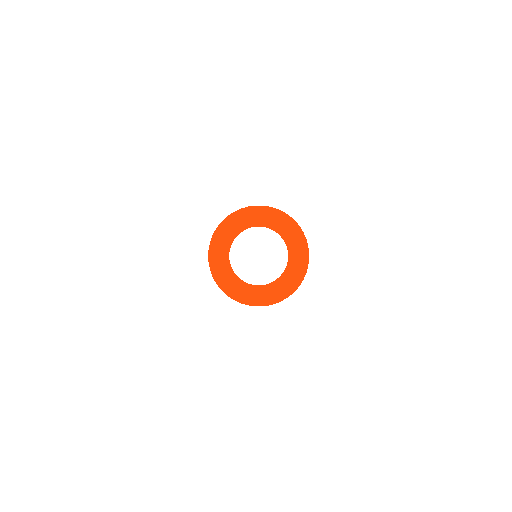
VHTR Generator
- Production of hydrogen in a nuclear fission reactor that works at 1,000° through the uranium cycle
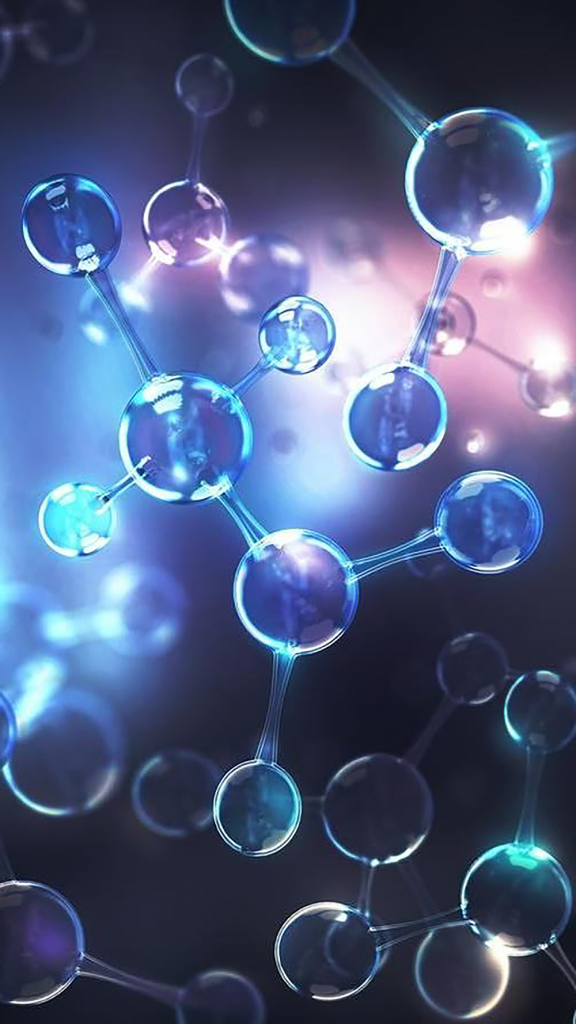
There is a deep interest in promoting a greener future, highlighted by the 196 nations that ratified the 2015 Paris climate agreement. The final document of the “International Climate Conference” highlights that the remedy for environmental stress requires limiting emissions of greenhouse gases (carbon) as soon as possible and to contain the global temperature increase in this century to a maximum of 2 ° C, indeed possibly not to exceed 1.5 ° C.
Hydrogen offers an effective solution to this problem. As a highly flexible energy carrier, hydrogen can provide a clean, integrated and multisectoral approach to energy needs, making a decisive contribution to protecting the earth’s energy future.
Hydrogen: the current scenario
H2 Production
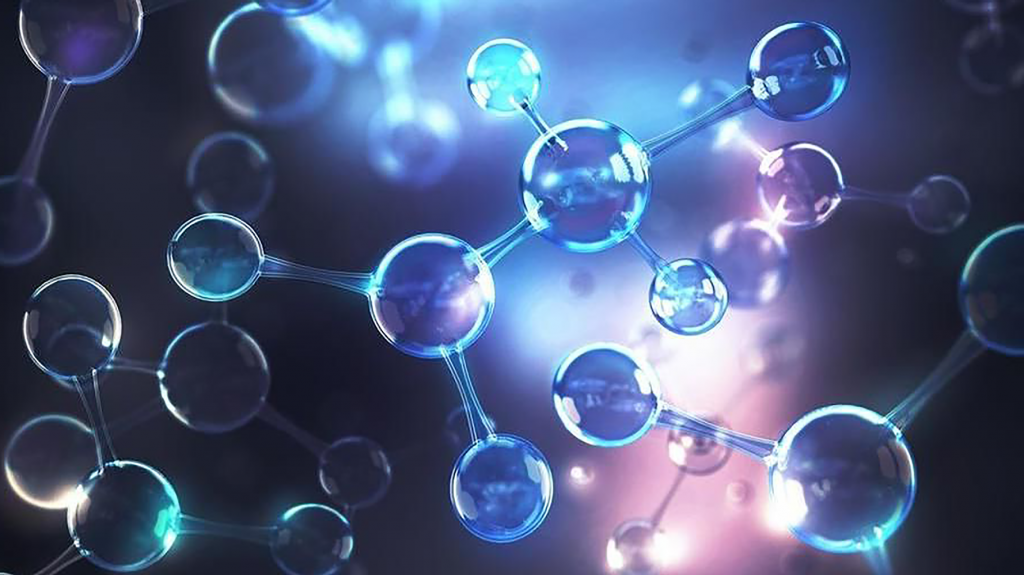
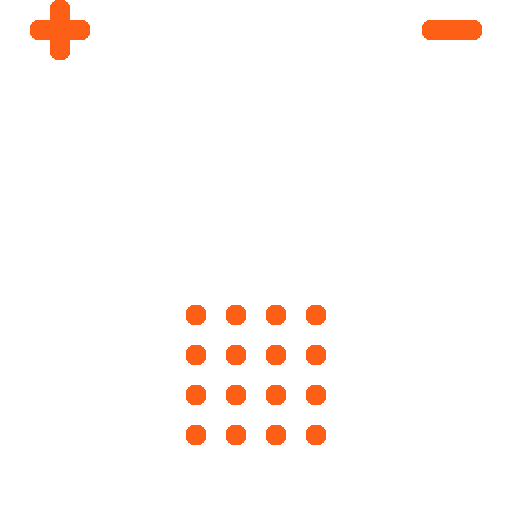
Electrolysis of water
- Highly energy-intensive process (high consumption of electricity to ensure the reaction)
- Use of large quantities of water (a resource that is becoming increasingly important)
- High cost of production (about 2,37 $ / Kg
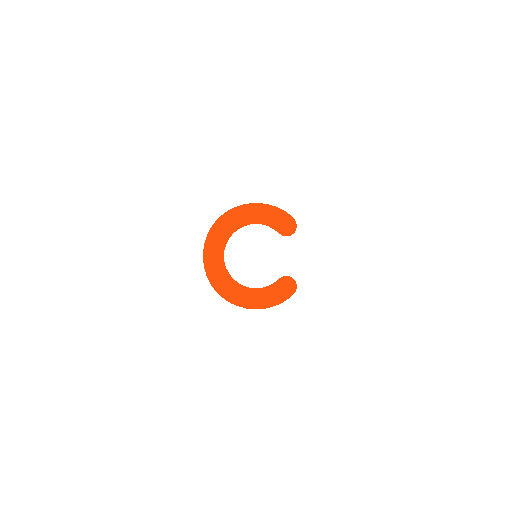
Methane steam reforming
- Process that involves the use of non-renewable fossil resources in high quantities (about 2Kg of CH4 for each Kg of H2)
- Reduced production cost (about $ 0.40 / Kg)
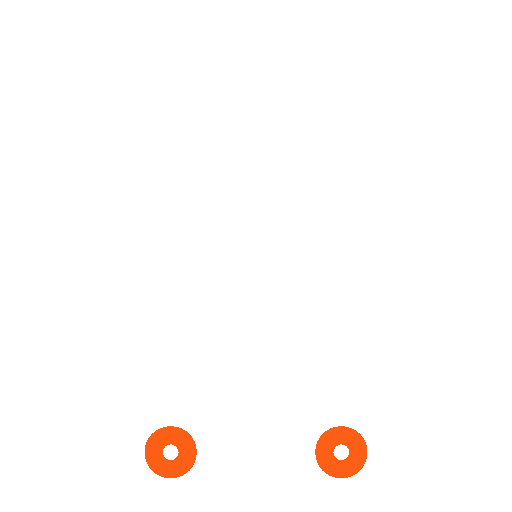
Coal gasification
- Process that involves the use of non-renewable fossil resources
- Low production cost (about 0,54 $ / Kg)
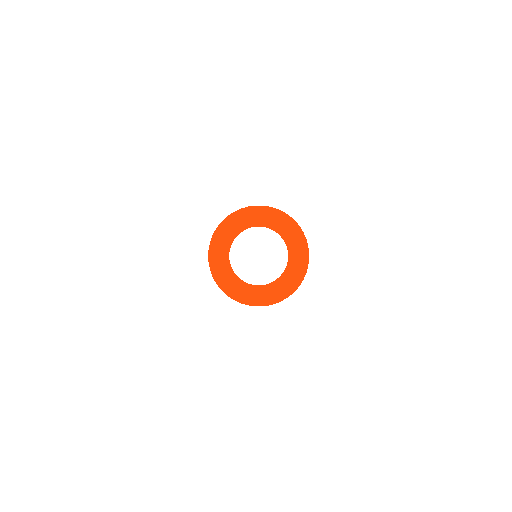
VHTR Generator
- Production of hydrogen in a nuclear fission reactor that works at 1,000° through the uranium cycle
There is a deep interest in promoting a greener future, highlighted by the 196 nations that ratified the 2015 Paris climate agreement. The final document of the “International Climate Conference” highlights that the remedy for environmental stress requires limiting emissions of greenhouse gases (carbon) as soon as possible and to contain the global temperature increase in this century to a maximum of 2 ° C, indeed possibly not to exceed 1.5 ° C.
Hydrogen offers an effective solution to this problem. As a highly flexible energy carrier, hydrogen can provide a clean, integrated and multisectoral approach to energy needs, making a decisive contribution to protecting the earth’s energy future.
Hydrogen: the current scenario
H2 Production
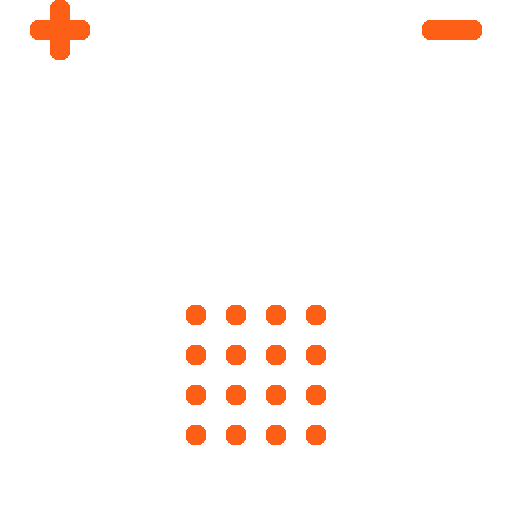
Electrolysis of water
- Highly energy-intensive process (high consumption of electricity to ensure the reaction)
- Use of large quantities of water (a resource that is becoming increasingly important)
- High cost of production (about 2,37 $ / Kg)
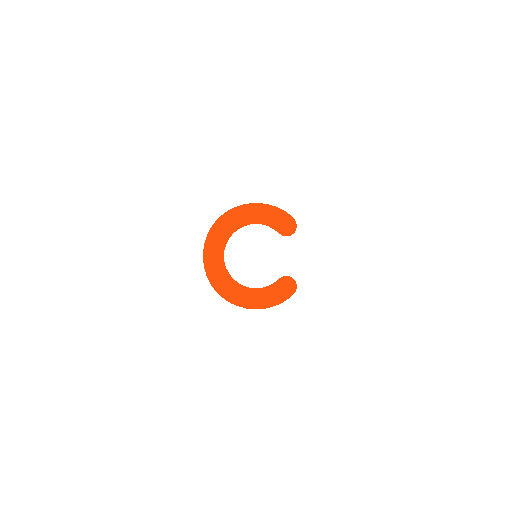
Methane steam reforming
- Process that involves the use of non-renewable fossil resources in high quantities (about 2Kg of CH4 for each Kg of H2)
- Reduced production cost (about $ 0.40 / Kg)
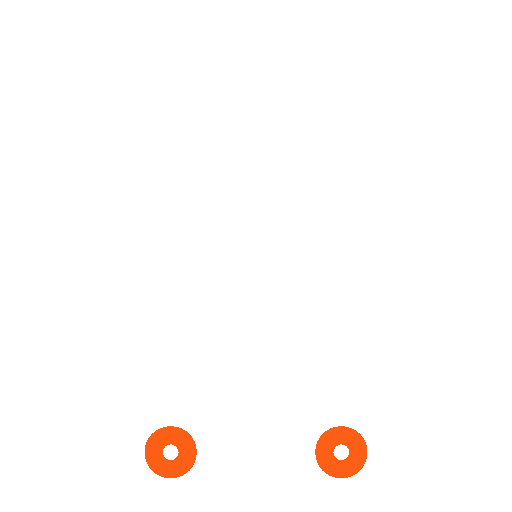
Coal gasification
- Process that involves the use of non-renewable fossil resources
- Low production cost (about 0,54 $ / Kg)
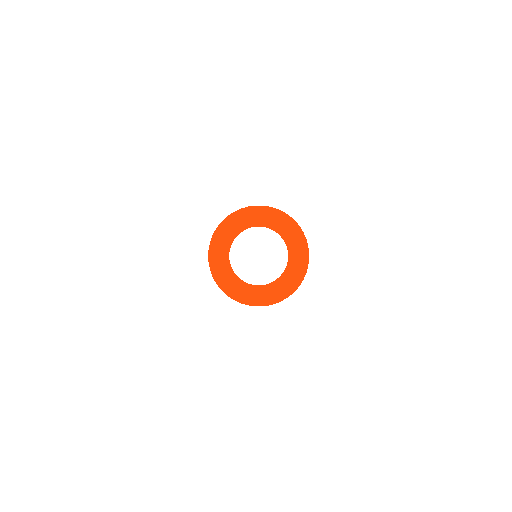
VHTR Generator
- Production of hydrogen in a nuclear fission reactor that works at 1,000° through the uranium cycle
There is a deep interest in promoting a greener future, highlighted by the 196 nations that ratified the 2015 Paris climate agreement. The final document of the “International Climate Conference” highlights that the remedy for environmental stress requires limiting emissions of greenhouse gases (carbon) as soon as possible and to contain the global temperature increase in this century to a maximum of 2 ° C, indeed possibly not to exceed 1.5 ° C.
Hydrogen offers an effective solution to this problem. As a highly flexible energy carrier, hydrogen can provide a clean, integrated and multisectoral approach to energy needs, making a decisive contribution to protecting the earth’s energy future.
The hydrogenesys opportunity: our proposal
HydroGenesys goes beyond the concept of disposal and reinterprets it in TRANSFORMATION through a cycle that does not involve incineration / waste-to-energy processes but a high-temperature pyrolysis reactor in a closed-cycle process, completely self-sustained in terms of energy (some external resources are only needed for the start-up phase) and does not release any polluting component (solid, liquid or gaseous) into the atmosphere.
The high temperature pyrolysis process, as engineered in our plants, breaks down organic materials (recyclable or not) into chemically simpler by-products which, processed in post-processing, return quality Hydrogen (H2), Carbon Dioxide (CO2) food, thermal energy and vitrified aggregates.
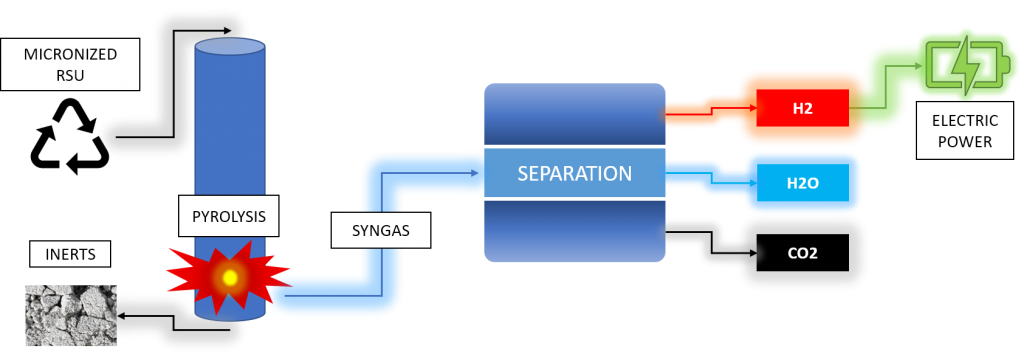
The hydrogenesys opportunity: our proposal
HydroGenesys goes beyond the concept of disposal and reinterprets it in TRANSFORMATION through a cycle that does not involve incineration / waste-to-energy processes but a high-temperature pyrolysis reactor in a closed-cycle process, completely self-sustained in terms of energy (some external resources are only needed for the start-up phase) and does not release any polluting component (solid, liquid or gaseous) into the atmosphere.
The high temperature pyrolysis process, as engineered in our plants, breaks down organic materials (recyclable or not) into chemically simpler by-products which, processed in post-processing, return quality Hydrogen (H2), Carbon Dioxide (CO2) food, thermal energy and vitrified aggregates.
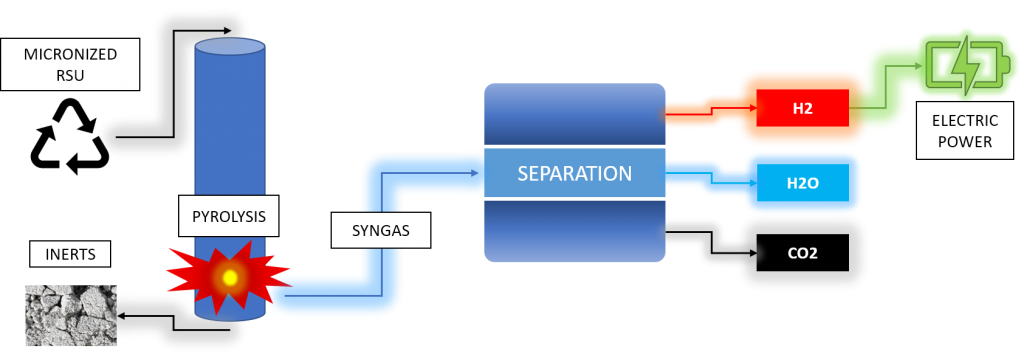
The hydrogenesys opportunity: our proposal
HydroGenesys goes beyond the concept of disposal and reinterprets it in TRANSFORMATION through a cycle that does not involve incineration / waste-to-energy processes but a high-temperature pyrolysis reactor in a closed-cycle process, completely self-sustained in terms of energy (some external resources are only needed for the start-up phase) and does not release any polluting component (solid, liquid or gaseous) into the atmosphere.
The high temperature pyrolysis process, as engineered in our plants, breaks down organic materials (recyclable or not) into chemically simpler by-products which, processed in post-processing, return quality Hydrogen (H2), Carbon Dioxide (CO2) food, thermal energy and vitrified aggregates.
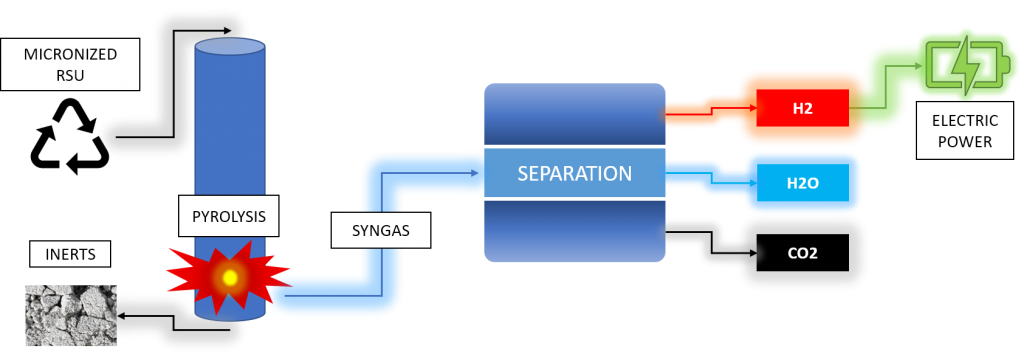
Certifications
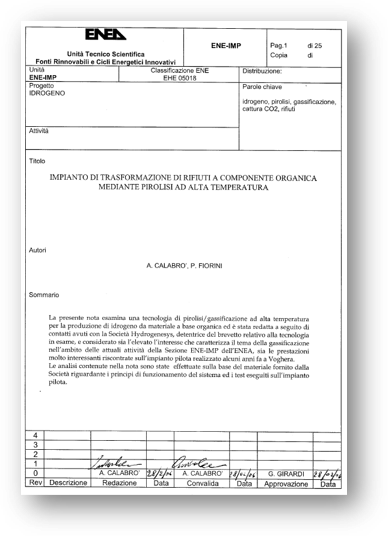
ENEA Certification
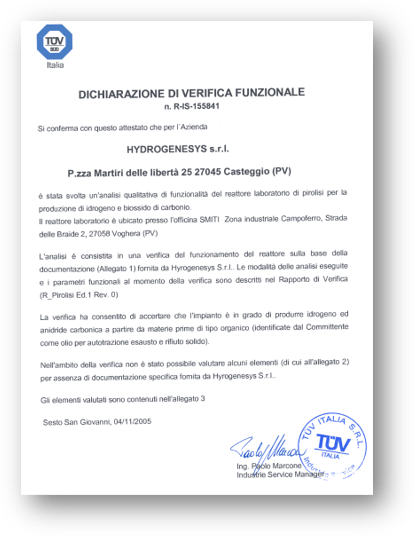
TUV Certification
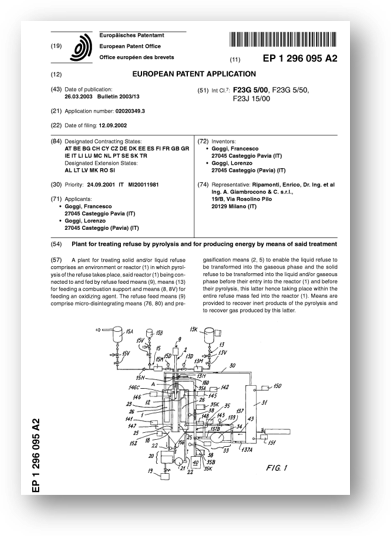
EU Patent
The hydrogenesys opportunity: business model
The current development and the agreements in place in various European and non-European countries puts us in the position of being able to propose a financing operation that is certainly interesting.
The project underlying the proposed investment includes the sale of pre-agreements with suppliers of raw materials / buyers of finished products which will be defined and signed upon payment of the first installment of the loan.
The construction of the plant, whose remuneration will take place in monthly SALs, will last 12-18 months. Its commissioning, including the set up and start up operations that will make the plant ready and productive, will be completed within the deadline of 24 months.
The forecast business plan, developed in accordance with the requirements of Deutsche Bank, demonstrates the plant’s ability to pay back the investment within a period of 33 months.
The hydrogenesys opportunity: business model
The current development and the agreements in place in various European and non-European countries puts us in the position of being able to propose a financing operation that is certainly interesting.
The project underlying the proposed investment includes the sale of pre-agreements with suppliers of raw materials / buyers of finished products which will be defined and signed upon payment of the first installment of the loan.
The construction of the plant, whose remuneration will take place in monthly SALs, will last 12-18 months. Its commissioning, including the set up and start up operations that will make the plant ready and productive, will be completed within the deadline of 24 months.
The forecast business plan, developed in accordance with the requirements of Deutsche Bank, demonstrates the plant’s ability to pay back the investment within a period of 33 months.
The hydrogenesys opportunity: business model
The current development and the agreements in place in various European and non-European countries puts us in the position of being able to propose a financing operation that is certainly interesting.
The project underlying the proposed investment includes the sale of pre-agreements with suppliers of raw materials / buyers of finished products which will be defined and signed upon payment of the first installment of the loan.
The construction of the plant, whose remuneration will take place in monthly SALs, will last 12-18 months. Its commissioning, including the set up and start up operations that will make the plant ready and productive, will be completed within the deadline of 24 months.
The forecast business plan, developed in accordance with the requirements of Deutsche Bank, demonstrates the plant’s ability to pay back the investment within a period of 33 months.